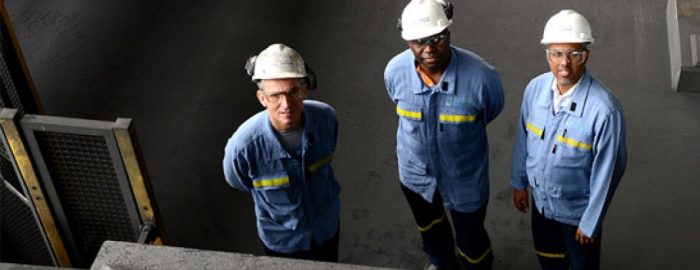
Technology
The reduction plant, where the actual liquid metal production takes place constitutes the main part of the Qatalum smelter. The annual capacity is 640.000 tons of liquid Aluminium.
The Reduction Plant is where Aluminium metal is “reduced” from alumina (Aluminium oxide) through electrolysis.
The Qatalum plant is a comprehensive Aluminium production facility that includes a Reduction Plant, Carbon Plant, and a Cast house, together with a dedicated Power Plant, various utilities and port and storage facilities.
The Reduction Plant, where Aluminium is produced, features advanced aluminum reduction technology from Hydro Aluminium. The two parallel 1 km pot rooms house two rows of electrolytic cells containing a total of 704 pots.
The carbon plant manufactures carbon anodes, which are a vital part of the primary Aluminium production process. It consists of a paste plant and an anode baking plant. The carbon plant has a capacity to produce approximately 350,000 tons of anodes per year for use in the reduction plant.
The Carbon Plant, which produces rodded carbon anodes for use in Reduction, includes a paste plant, anode baking plant and a rodding shop and two bath cleaning plants.
The Qatalum C​asthouse produces 670,000 tons of casthouse products per year. Its main products are extrusion ingots and foundry alloys. The casthouse also houses equipment for producing standard primary ingots.
The Cast house, where liquid metal is transformed into high quality Aluminium products, produces extrusion ingots (including precision tubing alloys), foundry alloys and standard ingots for customers around the world.
The Qatalum power plant is a combined-cycle power plant with the capacity to supply 1350 MW to the Aluminium plan​t.
The Power Plant features 4 gas turbines and 2 steam turbines operating in a combined cycle supplying up to 1350 MW to the Aluminium Plant. A recent investment on GE’s latest technology of Advanced Gas Path components has reduced the CO2 greenhouse gas emissions of the gas turbines and increased the Energy efficiency of the plant to 53%. Power plant condenses the Low-Pressure Steam from the turbines using a Large Cooling Tower, hence optimizing the consumption of water in the entire water-steam cycle.
Occupational Health, Safety and Environmental management system and Quality management system certification milestones.
Quality Management System (QMS) is defined as a structured system that documents processes, procedures, and responsibilities for continuously delivering high-quality products and services that meet regulatory and customer requirements. The objective of a quality management system is to provide a framework that improves communication, collaboration, and consistency across the organization while also reducing waste, and promoting continuous improvement
Aluminium is a sustainable material and as such has to be considered over its full life cycle. It is used in all sorts of applications: vehicles, aero planes, buildings, packaging and in various other applications.
Compared to many other materials, Aluminium has a lower weight, and therefore contributes to lower fuel consumption and emissions. It preserves food quality and reduces the need for building maintenance, while increasingly helping to save the energy used for cooling or heating purposes.
Aluminium production​
Primary Aluminium production has made significant progress when it comes to energy efficiency and reduced emissions. Modern production technology, such as that utilized in Qatalum, uses approximately 25 percent less energy than the average cell back in 1990.
Qatalum employs all the best available technologies in its processes, and has very little impact on the local environment (EIA Summary).
Emissions of greenhouse gases from modern technology, such as that used by Qatalum, are down to a minimum. Emissions of perfluorocarbons (PFCs) are less than 0.3 kg per tons of Aluminium produced, which is far below the global average.
Aluminium in use
The main end-use areas for Aluminium are transportation, construction, packaging and general engineering. Aluminium in cars reduces their weight and hence fuel consumption and emissions.
Studies show that one kilogram of Aluminium used in a car replaces two kilograms of heavier materials like iron or steel, reducing total emissions over the life-time of the car by 20 kg of CO2. The same applies for other vehicles such as trucks, buses, trains, etc. Aluminium used as packaging forms a complete barrier and thus helps preserve food, drink and pharmaceutical products.
Aluminium used in buildings can reduce the volumes of energy required for cooling or heating purposes. So-called intelligent facades can reduce energy consumption by up to 50 percent. This is important as buildings, both commercial and residential, represent more than 30 percent of energy consumption in Europe, more than each of the two sectors transportation and industry.
Aluminium recycling
Almost every Aluminium product can be commercially, and even profitably, recycled at the end of its useful life. When recycled, Aluminium does not lose metal quality or properties. The challenge is often to recover the Aluminium. This is up to the various waste collection schemes often initiated and operated by local authorities.
More than 90 percent of the Aluminium in scrapped cars is recovered and recycled. The same high recycling rates have been observed for commercial buildings, where the value of Aluminium scrap is clearly recognized. For Aluminium beverage cans recovery and recycling rates exceed 90 percent. This is the case in several European countries. Aluminium recycling requires only five percent of the energy expended in primary Aluminium production.
Recycled Aluminium represents the metal source for more than one third of Aluminium production globally. Demand for recycled Aluminium is increasing even more strongly than that for primary Aluminium. In the Aluminium life cycle and value chain, recycling is key to a sustainable Aluminium future.